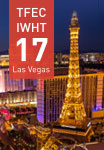
ISSN Online: 2379-1748
ISBN Flash Drive: 978-1-56700-469-4
ISBN Online: 978-1-56700-470-0
Second Thermal and Fluids Engineering Conference
A NUMERICAL MODEL OF A TWO-PASS, CROSS-FLOW CONFORMAL HEAT EXCHANGER FOR AEROSPACE APPLICATIONS
Abstract
Heat exchangers have seen widespread use in aerospace applications to properly manage aircraft and propulsion system heat loads. However, these heat exchangers are typically large (in terms of volume and weight relative to flowrate), non-conformal and costly to implement. There is motivation for heat exchangers to be better integrated into flow paths, both for packaging and performance improvements. Recent advances in additive manufacturing have presented the potential to create highly conformal and better optimized heat exchangers. These additively manufactured, flexible geometry heat exchangers have the potential to reduce pressure losses and increase thermal performance when compared to rectilinear, traditionally manufactured heat exchangers.
In this work, a computational tool was developed to predict the thermal-hydraulic performance of an annular two-pass, cross-counterflow heat exchanger. Area ruling was used to keep velocities nearly constant in the heat exchanger core. Computational tool outputs include heat transfer rate, outlet temperature, pressure loss characteristics, heat exchanger weight, and volume as a function of user-supplied geometric inputs. A brief optimization was performed across multiple mass flow rates to determine preferred designs. Pumping power and modified volume goodness were used to perform the optimization. Using the geometries provided by the computational tool, a heat exchanger will be manufactured using additive techniques and tested across a range of operating conditions. The experimental results will help validate the computational tool.
In this work, a computational tool was developed to predict the thermal-hydraulic performance of an annular two-pass, cross-counterflow heat exchanger. Area ruling was used to keep velocities nearly constant in the heat exchanger core. Computational tool outputs include heat transfer rate, outlet temperature, pressure loss characteristics, heat exchanger weight, and volume as a function of user-supplied geometric inputs. A brief optimization was performed across multiple mass flow rates to determine preferred designs. Pumping power and modified volume goodness were used to perform the optimization. Using the geometries provided by the computational tool, a heat exchanger will be manufactured using additive techniques and tested across a range of operating conditions. The experimental results will help validate the computational tool.